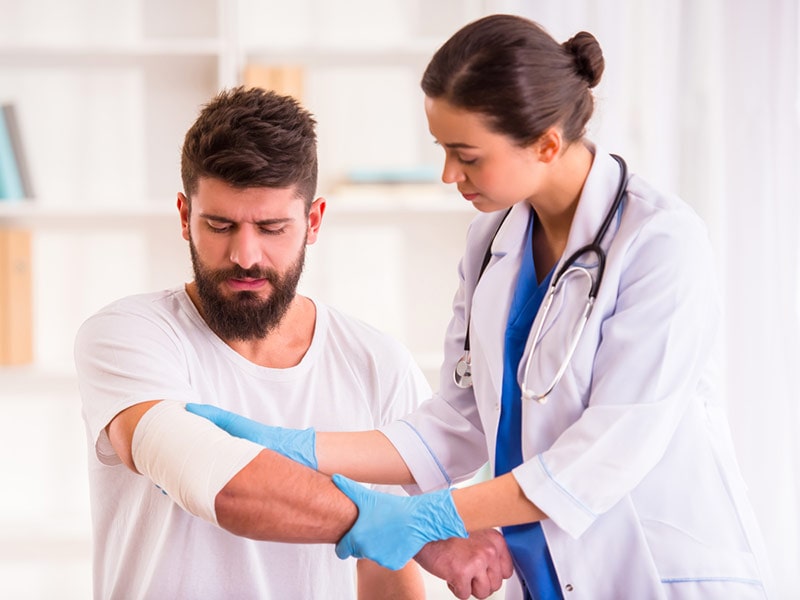
The concept of Occupational Health is defined as the different activities that promote and protect the health of workers in order to reduce the rate of accidents and illnesses produced by different occupational activities, both physical and psychological.
Fractures, cuts and strains, repetitive motion disorders, sight or hearing problems, illnesses caused by exposure to unhygienic or radioactive substances and work-related stress are some of the most common injuries and illnesses among construction workers; preventing them in time is the primary mission that each of the employers in the sector must have.
In this sense, the government issued decree 1072 of 2015 which unifies the norms related to work in Colombia and especially the obligations of employers with respect to their employees and the implementation of the Occupational Safety and Health Management System (OSH).
In this way all organizations that have at least one worker must comply with the regulations of the decree and implement the requirements of the same whose primary objectives are:
- Identify the dangers, evaluate and evaluate the risks, and establish the respective controls.
- Protect the safety and health of all members of the company.
- Comply with current standards on safety at work.
Main premises of decree 10272 for the construction sector:
- Before starting work, the employer must establish a risk balance that includes any risk of accident or possible acquisition of disease. Next, propose solutions to minimize such risk.
- The employer must leave in writing the policies to be established regarding occupational health and their objectives, and must also disclose them among all the members of the construction site.
- It must establish responsibilities within the team in charge of ensuring the safety of employees (in the case of construction, it must have personnel in charge of verifying that employees comply with the different standards established by the respective occupational safety plan).
- Periodic revisions should be carried out where the balances by period of time of the implementation of the safety system should be written down.
- Allocate adequate resources for the safety system to function (safety implements, helmets, boots, gloves, nets against falling debris, ETC safety harnesses).
- Make a good practices manual specifying the correct use of the different work tools, as well as the correct procedure in the different activities of the work.
- To keep workers informed of the corresponding regulations and their different updates, it is the employer’s duty to provide constant training to employees on the subject.
- To have personnel specialized in occupational health and safety in charge of planning, developing and implementing the OSH (Occupational Health and Safety Management System) hysterical.
Once the work project is finished, the employer must draw the conclusions and carry out a final evaluation that must include:
- Legal Matrix
- Hazard Identification Matrix
- Vulnerability analysis
- Emergency Plan
- Evaluation of control measures
- Compliance with the training program
- Evaluation of the work center
- Evaluation of epidemiological programmes
- Diseases and accidents statistics
- Indicator risk
- Diagnosis of employee health conditions (before and after hiring)
Resolution 1111 of 2017
This resolution establishes the minimum standards for implementing the Occupational Safety and Health Management System (OHSMS) for employers and contractors, which will have the right to receive official recognition from the Ministry of Labor where it is established in writing compliance with the minimum standards.
On the other hand, the decree also provides for penalties in the form of fines for those who do not comply with the provisions of the resolution, these are contemplated in Law 1562 of 2012 and Decree 1295 of 1994 and which can range from 500 legal minimum monthly wages in force to 100 SMMLV.
Working at heights
Work at heights is considered to be of high risk because this activity is one of the ones with the highest percentage of accidents in construction works, in Colombia this work is governed by Resolution 1409 of 2012 document which establishes safety regulations for protection against falls in work at heights and which is applicable to all employers, companies, contractors.
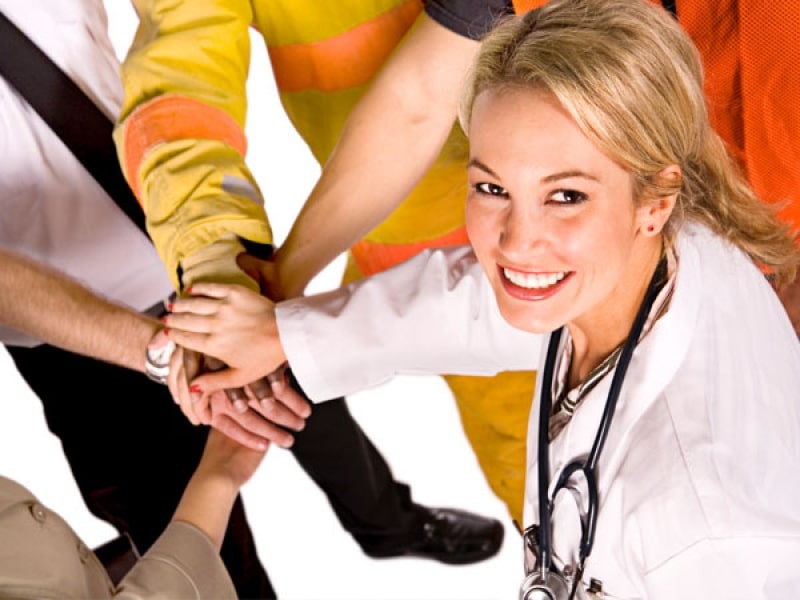
Subcontractors and in general to all companies that develop work at heights with danger of falls greater than 1.50 meters except emergency and rescue activities and recreational activities, sports, high mountain or related.
The resolution defines aspects as:
Definitions
Anchorage: Safe point to which personal fall protection equipment can be connected.
Equipment Approval: Document written and signed by a qualified person, issuing their concept of compliance with the manufacturer’s requirements.
Safety Assistant: employee assigned to control that the safety action plans at heights are fully complied with, this must be properly trained and certified.
Training Center: place where training will be provided on the correct way to handle tools at height, this must have certified fall protection equipment, including vertical and horizontal lifelines, whether portable or fixed and all resources to ensure adequate training of the worker.
Certificate of labor competence: Document issued by a certifying body invested with legal authority for its issuance, which recognizes the labor competence of a person to perform in that activity.
Training certificate: Document issued at the end of the process that certifies that a person has completed and passed the necessary training to perform a work activity. This certificate does not expire.
Obligations of the employer
- Conduct medical evaluations.
- Perform a fall protection program.
- To cover the conditions of risk of fall in work at heights by means of control measures against falls of persons and objects.
- To guarantee that the measures taken, systems and equipment comply with the requirements of this resolution of the Occupational Health and Safety Management System (OHSMS).
- Have a work coordinator at heights.
- Provide equipment, training and retraining, this should have no cost to the employee.
- Conduct an annual retraining for each employee.
- Request the tests that guarantee the proper functioning of the fall protection system and/or the certificates that endorse it.
- Do not allow minors or pregnant women to work at heights.
- Have a rescue plan with resources and trained personnel.
Employee obligations
- Attend employer-programmed trainings and pass evaluations.
- Reporting any type of disability or illness that prevents you from working at heights.
- Report damages or deteriorations or failures of established prevention mechanisms.
Requirements for prevention measures
- Engineering systems: Systems related to changes in design, assembly, construction, installation, commissioning to eliminate or mitigate the fall.
Fall Mitigation Program
- Collective prevention measures: all activities aimed at informing or demarcating the danger zone and avoiding a fall from heights or being injured by objects.
- Signposting of branded areas.
- Access control, orifice management.
- Passive measures: designed to stop or capture the worker in the trajectory of his fall (net).
- Active protection measures: involve the participation of the worker, training, certifications in safety procedures at heights.
- Material: all elements, ropes, beams, boards, ETC scaffolds must have a minimum strength of 500 pounds.
Working in trenches
The work carried out in trenches and excavations are of high risk for the construction sector. Hence the importance of accident prevention measures.
Risks:
- Falls in the ditch.
- Landslides.
- Emission of gases.
- Contact with biological agents (viruses, bacteria, fungi).
- Poor quality stowage.
- Fall of tools or heavy machinery.
- Moisture in the soil.
- Cables, tubes or anything that is not referenced in the planning.
Recommendations for work in trenches
- Use protective equipment such as gloves, helmets, masks, hearing protectors, goggles, safety footwear and appropriate clothing for each job within the work.
- Place the extracted material at least 2.50 mt away from the trench, the tools and equipment used must be 0.60 m from the edge of the trench.
- Do not use heavy machinery and workers inside the trench at the same time.
- Make constant maintenance of work tools.
- Have trained personnel who constantly assess that safety standards are being met.
- Occupational Diseases
Workers in the construction sector are exposed to many factors that can generate diseases, extreme temperatures, height changes, handling of dangerous equipment, days of more than 10 hours, noisy areas extreme noise zones, constant dust, humidity etc..
These circumstances generate diseases such as: silicosis, by inhalation of silica and sand; calicosis, by exposure to cement; professional deafness, musculoskeletal disorders due to repetitive movements (lumbago of mechanical origin, shoulder pain and discopathies, among others) and other pathologies associated with exposure to vibration.